特别策划
您当前的位置:首页 >> 特别策划
“再制造”概念纠偏:大修≠再制造
更新时间:2014-12-02
摘要: | 目前我国再制造产业发展尚处于起步阶段,再制造作为新的理念还没有被消费者及社会广泛认同,应当从扩大再制造应用领域、培育再制造示范企业、规范旧件回收体系、开拓国内外市场着手,加强法规建设,强化政策引导,逐步形成适合我国国情的再制造运行机制和管理模式,实现再制造规模化、市场化、产业化发展。 |
文|陈雪芹 梁玲 胡雪峰
金色的秋阳暖暖地照射在中国石油集团济柴动力总厂再制造中心(以下简称济柴再制造中心)近16万平方米的厂区内,也暖暖地照进济柴人的心头。在这个厂区内,一台台再制造的“新”设备犹如一颗颗饱满的果实,让济柴人充满了丰收的喜悦。这种喜悦源于济柴人对再制造前景的美好期待。
尽管再制造前景可期,但在济柴再制造中心副总经理刘志伟看来,国人对再制造的理解还有待深入,许多人通俗地把再制造理解为对设备的简单翻新,这种对再制造认识的误区,对产业发展十分不利。他认为,国家应从节能、环保等政策方面加大对再制造的扶持力度。
再制造,这个有利于低碳发展的产业,在发达国家早已得到蓬勃发展。美国密歇根州理工大学研究表明,生产再制造产品减少86%能源消耗,减少93%水耗,减少99%的废气物填埋空间,减少61%温室气体排放量。
我国在宏观层面支持再制造发展的政策有据可查。从2005年开始,国务院提出要支持机电产品的再制造,“再制造”这个词逐步地引入到中国,虽然老百姓对再制造仍比较陌生。2005年,国务院印发的《关于加快发展循环经济的若干意见》明确提出支持废旧机电产品再制造。2008年,《循环经济促进法》将再制造纳入法律范畴进行规范,为推进再制造产业发展提供了法律依据;国家发展改革委推出了第一批14家汽车零部件试点单位; 2009年,工信部推出第一批35家机电产品再制造试点单位名单;2010年,国家发展改革委联合11个部门颁发《关于推进再制造产业发展的意见》;2011年,“十二五”发展计划明确提出支持发展再制造;2012年,国家主席习近平访美期间,在中国经贸合作论坛开幕式上的发言中指出:拓展合作领域,培育新的经贸增长点,加快推动再制造等新兴领域开展合作;2013年,国务院办公厅发布的《国务院办公厅关于加强内燃机工业节能减排的意见》指出,推动再制造产业发展,降低内燃机燃油消耗率,提高我国内燃机产品的节能减排水平和内燃机工业的国际竞争力。同年,工信部印发《内燃机再制造推进计划》,确定到“十二五”末内燃机工业再制造生产能力、企业规模、技术装备水平显著提升。
制造产业是将原材料生产加工成为产品的一种生产活动的统称,再制造产业是指在原有产业的基础上,将废旧产品利用技术手段进行修复和改造的一种产业。它是以产品全寿命周期理论为指导,以实现废旧产品性能提升为目标的一种产业。再制造产业应用领域主要涉及汽车零部件、工程机械、机床、大型工业装备、国防装备、铁路设备、农用机械、医疗设备和办公设备等领域。
再制造,这个在我国尚属起步初期的产业,在促进生态文明的建设中,究竟发挥着怎样的作用?它的前行之路还面临着怎样的障碍?
绿色产业蹒跚前行(上篇)
“在国家鼓励发展循环经济的大背景下,再制造产业产生的节能环保效果还需强化宣传,目前许多再制造企业投入大但吃不饱。”河北省沧州市设备管理协会副秘书长吉卫华感慨地说。
我国的再制造产业发展至今已经10年有余。在实践的基础上,逐步探索形成了以高新技术为支撑、产学研相结合、既循环又经济的自主创新的中国特色再制造模式。2000年,由12位中国工程院院士和12位专家组成的咨询项目课题组结合国情,提出再制造工程的概念并引进了系统的论证,完成了中国工程院2000年咨询项目"绿色再制造工程及其在我国的应用前景"报告。
“我国再制造产业的发展还面临突出问题,它尚处于起步阶段。再制造的意义目前还没有被社会广泛认同,往往投资大、收入慢、利润小。”刘志伟意味深长地说。
节能环保效果显著
在一些奔驰、宝马等品牌车的4S店,同一款车型可能有两种价格,而且价格相差会在15%以上。车价便宜的是因为汽车发动机等总成零部件采用的是“再制造”产品。 这样的场景在不久的将来或将出现在更多的4S店。
再制造不仅节约资源,减少环境污染,也能让企业或消费者得到实惠。济柴再制造中心研究结果显示,若一台柴油机按新机+大修+大修+大修报废与再制造机+再制造+再制造+再制造+再制造的使用模式相比,则相同4.8万小时节约投资:33.77万元 *4.8万小时=162.096万元。
再制造的产品与新品相比较: 节约成本50%以上,节能达到60%以上,节材70%以上,污染物排放降低80%以上,而每生产100台济柴再制造发动机可节约金属480吨,节约标准煤312吨,节约水10万吨。使用一台再制造机与大修机相比平均万小时节省548.97万元-515.20万元=33.77万元以上,经济效益显著。这将有力促进资源节约型、环境友好型社会的建设。
大修机≠再制造机
究竟什么是再制造?在对济柴再制造中心进行调研后,再制造的概念逐渐变得清晰——再制造绝不是简单的翻新,国人对再制造产业的认识还存在误区。
再制造需要先进的设备支撑。在济柴再制造中心的厂区内, 该中心综合管理部主管韩景伟兴致勃勃地为记者介绍着车间先进的设备——完备的绿色环保清洗设备、无损检测诊断设备以及前沿的尺寸修复技术等,彰显出济柴再制造中心卓越的再制造能力。
再制造需要先进的工艺流程。由于再制造使用的是经过长期服役而报废的各种成型零件,其损伤失效形式复杂多样,残余应力、内部裂纹和疲劳层的存在导致寿命评估与服役周期复杂难测,再制造还要在保持废旧零(部)件材质和形状基本不变的前提下,采用高技术恢复原产品的尺寸标准、达到或超过原产品的性能指标、实现原产品的功能升级。同时也采用正规化、规模化的加工手段,因此加工工艺更为复杂。
吴成武被誉为济柴再制造中心年轻的专家,从事再制造技术研究与应用工作多年,他向记者介绍了发动机再制造的主要工艺流程和产品分类。济柴对旧发动机进行再制造主要分为三种类型, 一是恢复型再制造:即老旧的发动机按原型机标准再制造,达到原新机的性能及排放标准;二是升级型再制造:即按现新机的标准进行再制造升级和改进,达到现新机性能和排放标准;三是改装型再制造:即将旧机再制造改装为其他机型,如将柴油发动机再制造为天然气机、双燃料机或重油机等其他机型,满足不同用户的差异化需求。
那么,经过再制造的设备与大修过的设备有何本质的不同?济柴再制造中心提供的台架试验数据显示,大修机燃油消耗率和机油消耗率均高于再制造机8~ 10%,而功率则要比再制造机低10%。大修机使用寿命10000小时,再制造机可相应承诺延长使用寿命至18000小时,即使用寿命达到新机首次大修的使用寿命。根据多年来统计,一台新柴油机60%负载率万小时耗柴油617.6吨,平均万小时柴油费用=617.6吨*0.8万元/吨=494.08万元,平均万小时机油费用=7.2吨*1.4万元/吨=10.08万元。而再制造机油耗则等同新机。
大修机油耗通常高于新机8~10%,大修机万小时耗柴油=新机上浮8%=667t,平均万小时柴油费=新机柴油费上浮8%=533.6万元,
平均万小时机油费=9吨*1.4万元/吨=12.6万元。由此可见,正常生产一口井深4300米的钻井时,再制造机可节约成本413.82万元-378.91万元=34.91万元。
装甲兵工程学院装备再制造技术国防科技重点实验室徐滨士院士介绍说,中国特色的再制造工程可以简单概括为:再制造是废旧产品高技术修复、改造的产业化。中国特色的再制造工程是在维修工程、表面工程基础上发展起来的,主要基于复合表面工程技术、纳米表面技术和自动化表面技术,这些先进的表面技术是国外再制造时所不曾采用的。其重要特征是再制造产品的质量和性能不低于新品,成本只有新品的50%,节能60%,节材70%,对环境的不良影响与制造新品相比显著降低。先进表面工程技术在再制造中的应用,可将旧件再制造率提高到90%,使零件的尺寸精度和质量性能标准不低于原型新品水平,而且在耐磨、耐蚀、抗疲劳等性能方面达到原型新品水平,并最终确保再制造装备零部件的性能质量达到甚至超过原型新品,受到国际同行广泛认同与关注。
推广之难
“目前,再制造设备来源及再制造产品销售渠道还不够畅通;再制造技术和管理水平还有待提高,产品质量良莠不齐;有关管理制度亟需健全,技术标准还不完善;再制造产业缺乏政策激励”刘志伟如是说。
事实上,从事再制造产业绝非简单的投入可以做到。2011年,济柴再制造中心投资6000余万元,全面启动建设发动机再制造项目
2012年,首台再制造发动机成功下线,并完成了发动机从零件到部件再到整机的再制造。当年,该中心与与徐滨士院士为首的院士团队建立了院士工作站。为再制造项目的研发方向与思路方面起到了重要作用。
徐滨士认为,发展再制造还面临着以下问题。一是对再制造认识高度不够,观念尚未普及。再制造作为制造产品报废阶段高技术回收处理的新理念,在我国还没有被人们广泛认识,再制造企业和消费者对再制造发展的世界背景认识不清,缺乏大局观和危机意识。二是发展思路尚待清晰,缺乏创新和规范管理。有些企业直接按制造模式进行再制造,有些企业简单地将维修模式移植到再制造,认为扩大规模就是再制造,导致在指导实际生产过程中定位和目标不准确。同时,有些企业简单认为制造的标准就是再制造标准,没有充分认识到再制造对象和过程的复杂性,导致大部分企业在旧件检测、再制造毛坯修复等关键环节没有建立相应的质量控制体系。三是部分关键技术需要攻关和推广,相关设备尚未实现产业化生产。目前大部分再制造试点企业主要采用换件法和尺寸修理法进行再制造,导致再制造后产品非标件多,用户认可程度低,加工成本高,旧件再制造率低。特别是缺乏废旧零部件质量检测和寿命评估技术,影响了再制造产品的可靠性;缺乏先进的表面工程新技术,大量磨损的关键零部件无法修复,再制造产品的旧件再制造率低。
扶上马如何送一程(下篇)
事实上,我国对再制造产业的扶持力度正在不断加大。为实施好再制造“以旧换再”试点工作,根据《再制造产品“以旧换再”试点实施方案》的要求,近日,国家发展改革委、财政部、工业和信息化部、商务部、质检总局组织制定了《再制造产品“以旧换再”推广试点企业评审、管理、核查工作办法》和《再制造“以旧换再”产品编码规则》。这为进一步推动再制造的发展提供了政策保障。
但是,对于尚处于起步阶段的再制造产业而言,再制造还亟待政策的进一步呵护。“许多亟待更新升级的设备,还面临着流通瓶颈。比如,有些企业的旧设备想送到我们中心进行再制造,但手续繁琐缺少支持的,财务账也不好做。这种逆向物流缺乏财税政策的支持。”韩景伟说。
年轻的中国再制造产业
“我国的再制造产业尚处于起步阶段,发展还很不成熟。在美国,如果你建了汽车厂,就要在周边建一个再制造工厂。这是发展循环经济的必然要求。”刘志伟介绍说。
据业内人士介绍,欧美等发达国家的再制造产业较为成熟。仅美国的再制造商就有5万余家,人们对再制造产品的使用已经深入人心。在售后维修领域,再制造零部件占总数的90%以上,对没有再制造厂的汽车企业,大多数民众会拒绝购买使用他们的产品。20世纪30至40年代,为了走出经济萧条的困境,最早的再制造产业雏形在美国汽车维修行业中出现。至20世纪80年代初,美国正式提出“再制造”。此后,其它工业发达国家开始大力发展再制造产业。目前再制造在欧美发达国家已形成了重要产业。
我国的再制造产业起步较晚,是个只有“10多岁”的年轻产业。它落后美国近50年。徐滨士认为,与欧美等发达国家相比,中国再制造业起步较晚。经过将近10年来的大力推广,我国已进入到以国家目标推动再制造产业发展为中心内容的新阶段,再制造技术并不输于世界先进水平。
国内的再制造工业首先在汽车领域得到了发展。1994年,经国家有关部门批转,中国重型汽车集团公司与英国Sandwell公司于1996年合资创办了济南复强动力优先公司,专门从事重载汽车柴油发动机再制造。上海大众联合发展有限公司引进了德国大众发动机再制造技术和标准。再制造发动机再保证与新机一样的性能、质量、售后服务和索赔条件,并打上再制造产品的标记,作为上海大众纯正配件,已纳入上海大众汽车销售公司的销售及维修服务网络。
我国在2002年2月出版的全国干部学习读本“21世纪干部科技修养必备”一书中,明确要求工程师在设计产品时,把再制造作为一个目标,使产品的某些部件达到"再制造"的标准。目前,再制造工程在我国的基础理论研究处于起步阶段,尚未深入到再制造的生产实践中。“再制造基础理论与关键技术”已经通过立项,并与2002年被批准为国家自然科学基金重点项目。
自2005年开始,我国政府陆续出台了相关政策大力推进再制造产业的发展,建立了再制造市场的准入机制,规范、管理再制造相关企业。自此,我国再制造产业逐渐步入正轨。 据了解,国家发展改革委于2011年启动再制造产业示范基地建设工作,并选择长沙、张家港两地开展再制造产业示范基地前期工作。
而在技术层面,再制造产业也正在不断完善。据业内人士介绍,中国特色的再制造模式注重基础研究与工程实践结合,创新发展了中国特色的再制造关键技术,构建了废旧产品的再制造质量控制体系,保证了再制造产品性能质量和可靠性;注重企业需求与学科建设融合,提升企业与实验室核心竞争力;注重社会效益与经济效益兼顾,促进国家循环经济建设。
一座亟待挖掘的金矿
远远地望去,一片荒芜的草地静静地从济柴再制造中心的车间延伸开去。“这是我们未来的新厂区,届时,就连许多油田的叩头机也可以在这里翻新了。”刘志伟颇为自豪地介绍说。
中国再制造产业是一座亟待挖掘的金矿。据有关方面测算,预计到2015年,中国工程机械产品的报废量将到达100万台左右,全国役龄10年以上的传统旧机床将超过200万台,废汽车约500万辆,假若再制造比例为10%,那么再制造的产值规模就可到达1000亿元。
在石油装备、船舶领域和工程机械等市场,我国再制造需求巨大,据不完全统计,在用的泥浆泵2000余台,按每年10%进行再制造,则再制造泥浆泵数量为200台。每台泵的再制造价按平均40万计,则每年泥浆泵再制造市场达8000万元。
内燃机再制造也是一块“大蛋糕”。工业和信息化部去年发布的《内燃机再制造推进计划》指出,推动内燃机再制造产业规模化、规范化发展,促进内燃机工业形成循环型生产方式和消费模式。该计划提出到“十二五”末,内燃机再制造产业规模达到300亿元,内燃机再制造产品配套服务产业规模达到100亿元。计划提出,到“十二五”末,内燃机工业再制造生产能力、企业规模、技术装备水平显著提升。全行业形成35万台各类内燃机整机再制造生产能力,3万台以上规模的整机再制造企业6家到8家,3万台以下规模的整机再制造企业6家以上;增压器、发电机、启动机、机油泵、燃油泵、水泵等关键零部件规模化配套企业30家以上。该计划还要求,到“十二五”末,建立一批乘用汽车、中重型商用车、工程机械、农业机械、发电设备、船舶动力、石油机械、铁路机车等内燃机再制造示范工程。初步建立全行业旧件逆向物流体系,一批核心企业建成旧件回收网络系统。再制造成形及检测等共性关键技术在行业内广泛使用,内燃机再制造工艺、技术及装备达到国际先进水平。全行业实现年节约金属40万吨,节能35万吨标准煤,新增就业岗位2.5万个,降低终端消费者使用成本100亿元。
再制造期“顶层细心”呵护
“再制造旧件来源及再制造产品销售渠道不够畅通;再制造技术和管理水平不高,产品质量良莠不齐;有关管理制度急需健全,技术标准还不完善;再制造产业还缺乏政策激励。”刘志伟感慨地说。
在我国再制造发展的10多年内,相关政策不断推动着再制造的发展,特别是2010年5月,国家发展改革委、科技部、工信部、公安部、财政部、商务部等11个部委联合下发《关于推进再制造产业发展的意见》,指导全国加快再制造的产业发展,并进一步明确“十二五”时期我国再制造产业发展目标、重点任务和保障措施,这对促进再制造产业健康有序和快速发展起到极其重要的推动作用。
自去年以来,国家对再制造产业的支持明显提速。去年8月,国务院出台《关于加快发展节能环保产业的意见》,明确提出将开展再制造“以旧换再”;9月,国家发展改革委、财政部等联合发布《再制造产品“以旧换再”试点实施方案》;10月,国家发展改革委批复设立首批两家“国家再制造产业示范基地”;11月,工业和信息化部印发《内燃机再制造推进计划》……
鼓励和发展再制造产业时不我待。徐滨士认为,再制造工程以节约资源、节省能源、保护环境为特色,以综合利用信息技术、纳米技术、生物技术等高技术为核心,充分体现了具有中国特色自主创新的特点。再制造可使废旧资源中蕴含的价值得到最大限度的开发和利用,缓解资源短缺与资源浪费的矛盾,减少大量的失效、报废产品对环境的危害,是废旧机电产品资源化的最佳形式和首选途径,是节约资源的重要手段。再制造工程高度契合了国家构建循环经济的战略需求,并为其提供了关键技术支撑,大力开展绿色再制造工程是实现循环经济、节能减排和可持续发展的主要途径之一。
把再制造产业扶上马还须送一程。业内人士认为,目前我国再制造产业发展尚处于起步阶段,再制造作为新的理念还没有被消费者及社会广泛认同,应当从扩大再制造应用领域、培育再制造示范企业、规范旧件回收体系、开拓国内外市场着手,加强法规建设,强化政策引导,逐步形成适合我国国情的再制造运行机制和管理模式,实现再制造规模化、市场化、产业化发展。
建设美丽中国,就要走低碳发展的绿色循环经济之路! 徐滨士提出,基于国内外再制造产业发展基础,中国的再制造产业发展应围绕科技创新为本、全面建设再制造配套服务体系等,为再制造产业发展创造优良的环境,提供有力的支撑。他认为,一是积极争取国家有关部门的支持,在再制造产业基地建立良好的再制造经营环境;二是依托产业优势,完善再制造产业链;三是把再制造产业所需装备作为再制造产业发展的重要内容,发挥机械装备制造业优势,大力发展再制造装备研发和生产,逐步形成再制造关键设备生产研发体系;四是发挥区位以及物流优势,与国内外原厂生产商合作发展逆向物流,建立再制造产业发展所需的工程机械、机床、废旧汽车零部件等的逆向回收物流体系,形成适应再制造产业发展所需的旧件收集能力;五是在企业现有质量管理体系建设的基础上,进一步完善适应再制造的管理体系要求等。
下一条:抱歉暂无数据
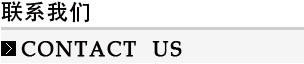
社长兼主编:陈雪芹
电 话:(010)68515135
编辑部
电 话:(010)68054816/68054837/68054838/68054839
运营部
电 话:(010)68052048
学术稿件咨询电话:
电 话:(010)64936065
新闻投稿邮箱:
zgsbgcxw@126.com
技术文章投稿邮箱:
zgsbgc@126.com
开户行
工行北京礼士路支行
户 名
《中国设备工程》杂志社
账 号
0200 0036 0902 2100 604
地 址
北京市西城区三里河一区12号楼4门3层(100045)